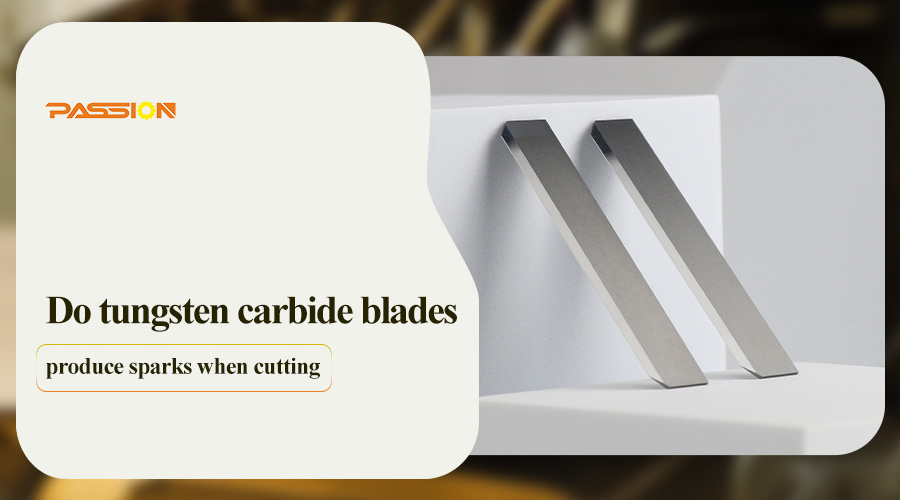
산업 제조 분야에서텅스텐 카바이드 블레이드고강도, 높은 경도 및 탁월한 내마모성으로 인해 절단 작업의 리더가되었습니다. 그러나 일반적으로, 절단 과정에서 산업용 블레이드가 고속으로 회전하고 금속 재료와 밀접하게 접촉하면 눈길을 끄는 현상이 조용히 발생합니다. 이 현상은 흥미로울뿐만 아니라 텅스텐 카바이드 블레이드가 절단 할 때 항상 스파크를 생성하는지에 대한 의문을 제기합니다. 이 기사에서는이 주제를 깊이 탐색하고 특히 텅스텐 카바이드 블레이드가 특정 조건에서 절단 할 때 스파크를 생성하지 않는 이유를 구체적으로 소개합니다.
텅스텐 카바이드 블레이드일종의 시멘트 탄화물로서 주로 텅스텐, 코발트, 탄소 및 기타 요소로 구성되어있어 물리적 및 화학적 특성이 뛰어납니다. 절단 작업에서 텅스텐 카바이드 블레이드는 날카로운 모서리와 고속 회전으로 다양한 금속 재료를 쉽게자를 수 있습니다. 그러나 규칙적인 상황에서 블레이드가 금속을 자르기 위해 고속으로 회전하면, 금속 표면의 작은 입자가 마찰에 의해 생성 된 고온으로 인해 점화되어 스파크를 형성합니다.
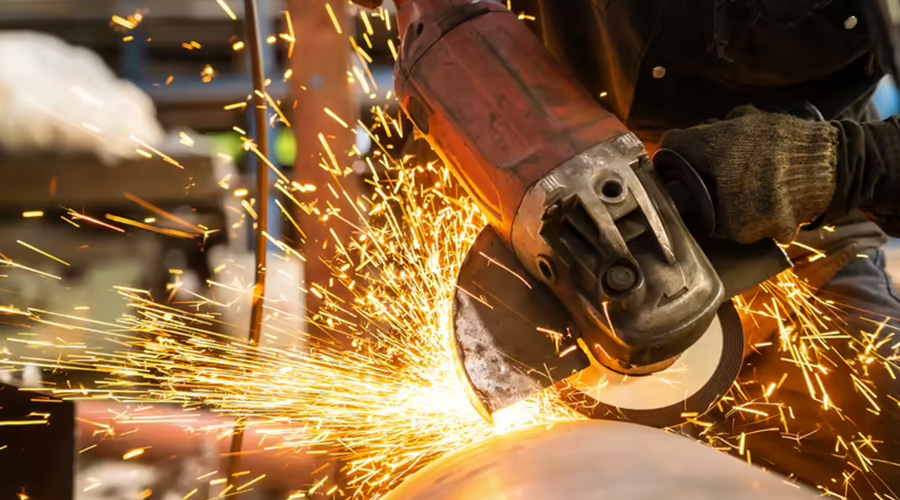
그러나 모든 텅스텐 카바이드 블레이드가 절단시 불꽃을 일으키는 것은 아닙니다. 텅스텐 카바이드 재료의 특수 비율 사용 또는 특정 절단 공정의 채택과 같은 특정 특정 조건에서 텅스텐 카바이드 블레이드는 스파크없이 절단 될 수 있습니다. 이 현상 뒤에는 복잡한 물리적 및 화학적 원리가 있습니다.
우선, 텅스텐 스틸 재료의 특수 비율이 핵심입니다. 텅스텐 카바이드 블레이드를 제조 할 때, 블레이드의 미세 구조 및 화학적 조성은 텅스텐, 코발트, 탄소 및 기타 요소의 함량과 비율을 조정하여 변경 될 수 있습니다. 이러한 변화는 절단 공정 동안 마찰 계수가 낮고 열전도율이 높은 블레이드를 초래합니다. 블레이드가 금속과 접촉 할 때, 마찰로 인해 발생하는 열은 블레이드에 빠르게 흡수되어 금속 표면의 작은 입자의 점화를 피하여 스파크의 생성을 감소시킬 수 있습니다.
둘째, 절단 과정의 선택도 중요합니다. 절단 과정에서 블레이드와 금속 사이의 마찰과 온도는 절단 속도, 절단 깊이 및 절단 각도와 같은 매개 변수를 조정하여 제어 할 수 있습니다. 절단 속도가 적당한 경우, 절단 깊이가 얕고 절단 각도가 합리적이며, 마찰과 온도가 크게 줄어들어 스파크 생성이 줄어 듭니다. 또한, 절단 영역을 냉각시키고 윤활하기 위해 냉각제를 사용하면 금속 표면의 온도를 효과적으로 감소시키고 마찰을 줄여 스파크 생성이 더욱 줄어 듭니다.
위의 이유 외에도, 텅스텐 카바이드 블레이드로 절단 할 때의 스파크 부족은 또한 금속 물질의 특성과 관련이있을 수 있습니다. 일부 금속 물질은 녹는 점과 높은 산화 저항성을 가지며, 이는 절단 과정에서 점화하기 쉽지 않습니다. 이 금속이 텅스텐 카바이드 블레이드와 접촉하면 일정량의 마찰과 온도가 생성 되더라도 스파크를 형성하기가 어렵습니다.
그러나 특별히 비례 한 텅스텐 강철 재료와 특정 절단 공정은 스파크 생성을 어느 정도 줄일 수 있지만 스파크를 완전히 제거 할 수는 없다는 점은 주목할 가치가 있습니다. 실제 응용 분야에서는 운영자의 안전을 보장하기 위해 보호 안경, 내화 의류 및 장갑 착용과 같은 필요한 안전 조치를 취해야합니다.
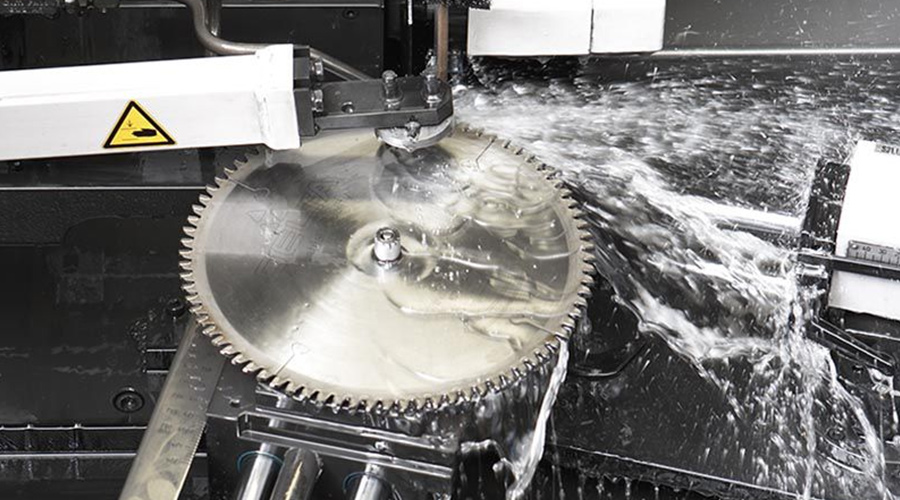
또한 가연성 및 폭발성 환경에서 절단 작업을 수행 해야하는 경우 폭발성 성능을 갖춘 절단 장비와 블레이드를 선택하여 화재 및 폭발의 위험을 줄여야합니다. 동시에, 절단 장비 및 블레이드의 정기적 인 검사 및 유지 보수가 양호한 작업 상태에 있는지 확인하는 것도 스파크 생성을 줄이는 데 중요한 조치입니다.
요약하든텅스텐 카바이드 블레이드절단이 요인의 조합에 의존 할 때 스파크를 생성합니다. 텅스텐 스틸 재료의 비율을 조정하고 절단 공정을 최적화하고 올바른 금속 재료 및 기타 측정을 선택함으로써 스파크 생성을 어느 정도 줄일 수 있습니다. 그러나 절단 작업의 안전성 및 효율성을 보장하기 위해 실제 적용에서 필요한 안전 보호 조치와 정기 검사 및 유지 보수 조치를 취해야합니다. 과학 기술의 지속적인 발전과 제조 공정의 지속적인 개선으로 인해 미래에는 스파크 생성을 줄이고 산업 제조 분야의 안전과 지속 가능한 개발을 촉진하기위한보다 혁신적인 기술과 조치가있을 것으로 믿어집니다.
나중에 정보를 계속 업데이트하고 웹 사이트 (PassionTool.com) 블로그에서 자세한 정보를 찾을 수 있습니다.
물론 공식 소셜 미디어에도주의를 기울일 수 있습니다.
시간 후 : 12 월 27 일 -2024 년